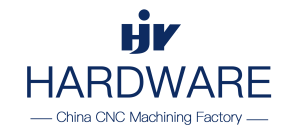
Anodising (also known as anodic oxidation) is an electrochemical procedure that change the metallic surface area right into a small oxide level. It's an electrolytic method which makes use of electrical up to create the oxide development impulse. The title anodising originates from the application program of damaging pole "anode" on the workpiece. Anodising stands out as the primary shielding therapy completed on aluminium. Additional metals which could easily be anodised are magnesium and titanium.
Anodizing of aluminium The original anodising procedure, created located in the 1920s 1930s, was influenced by chromic acid. This particular covering, known as chromic anodising, has become merely carried through beyond doubt certain sectors for instance army & aeronautics, as a result of the carcinogenicity of chromium salts.
At present, the most popular also popular anodising procedure is sulphuric acid based.
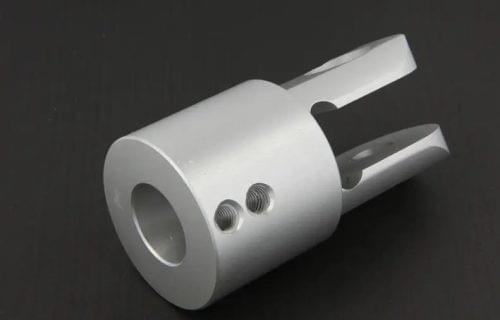
The components to become viewed are submerged within a twenty % sulphuric acid remedy, that functions as being an electrolyte. The damaging pole is used towards the aluminium portion, and the beneficial pole is attached to a cathode within the answer. When up is used on the electrolytic cellular, much needed oxygen ions acquire about the surface area on the workpiece which in turn, around conjunction with the aluminium atoms, develop a tough, small level of aluminium oxide with good qualities of:
oxidation resistance
put on resistance
hardness
uniformity of thickness
potential for colouring with pigments which penetrate the oxide layer
Dielectric insulation
Oxide level system Aluminium oxide, created by the procedure of anodising within sulphuric acid, features a microcrystalline honeycomb system, with hexagonal cells as well as a main porosity extending nearly all of the level. The difficult anodising procedure forms porosities having a diameter of aproximatelly 20 40nm along with a pore-to-pore distance of aproximatelly 100nm.
Aluminium oxide level structure
Aluminium oxide level structure
cross segment of aluminium oxide layer
scross segment of aluminium oxide layer
You will find 2 kinds of anodising, with various surface area qualities as well as various procedure parameters:
Kind of anodizing Characteristics
Decorative or natural Anodising
OX-A Used to offer excellent opposition to oxidation within moderate resistance and non-aggressive environments to put on as well as their chafing. Employed for ornamental uses because it could be coloured within an assortment of colors.
Tough anodizing
OX-HS - OX W Used on accuracy engineering components to offer very good oxidation as well as put on opposition, excessive resistance and hardness within intense locations.
Difficult Anodising of Aluminium The word difficult anodising identifies a compact and hard very aluminium oxide covering, with higher thicknesses compared to ornamental anodising. It's primarily utilized in accuracy aspects on machined areas from good, extruded, cast, rolled and die-cast components to boost oxidation opposition, hardness as well as put on opposition.
Specialized guide standards
The specialized specs and also overseas requirements associated with difficult anodizing are as follows:
Standards Title
ISO 10074 Anodizing of aluminium and the alloys of its - Specification for tough anodic oxidation coatings on aluminium as well as its alloys
MIL-A-8625 ANODIC COATINGS FOR ALUMINUM and ALUMINUM ALLOYS - Type III: Hard Anodic Coatings
UNI 7796 Rivestimenti a ossidazione anodica dell 'alluminio e leghe di alluminio - Ossidazione anodica a spessore - Requisiti e istruzioni generali di controllo
Visual look Hard anodising reproduces the counter morphology on the portion also it's thus easy to keep the area surface on the aluminium even with anodising (e.g. brilliant, satin, brushed, shot blasted, sandblasted, etc.).
The colour hinges a lot along the aluminium alloy utilized which enables it to differ in between greyish, deep greyish as well as brownish. The thickness influences the covering to grow darker as the thickness goes up. Alloys that contains a great deal of copper attain a bronze look as well as alloys containing plenty of silicon (> twelve %) could have an irregular colouring. Tough anodising, that has a deep color colour, is nicely suited in order to getting coloured with dim, opaque black and colours is generally selected, each for the excellent aesthetic appearance of its and then to equalise the colour inside the existence of various alloys.
Anodisable aluminium alloys All aluminium alloys are anodisable, with a few small exclusions. The best complications are came across with alloys that contain huge levels of components apart from aluminium, since it's just the aluminium which plays a role in developing the oxide level. Consequently, alloys that contain huge quantities of copper, such as for instance all those during the 2000 sequence, can't attain very high thicknesses and also the oxide level is going to be somewhat a lesser amount of compact as well as much less reluctant to wear and corrosion. Alloys that contain much more than twelve % silicon could reveal a lot less uniformity and thickness of the covering leading to a lesser amount of opposition to oxidation, put on and quite often irregular colour.
Anodising thickness
A unique thing about anodising will be the chance to jacket components having a uniform plus calibrated thickness on just about all surfaces. An different for this could be small diameter and extremely heavy gaps, for that the penetration capability on the covering should be evaluated separately.
The conventional thickness of tough anodizing is 30-50µm, but greater or lesser thicknesses may be selected based on certain requirements. Within the situation of extremely small tolerances, there's an inclination to reduce the anodising thickness and also to explain a tighter tolerance like 30±5µm.
Dimensional development The therapy thickness improves by fifty % outdoors as well as fifty % within the surface area on the aluminium portion. The radial dimensional boost is thus comparable to fifty percent the therapy thickness.
Oxidation opposition Hard anodising has a greater opposition to oxidation than ornamental anodising, as a result of the bigger thickness and also compactness on the oxide level. This particular opposition could be influenced by porosity inside the covering, and that is the original oxidation bring about. To be able to rise oxidation opposition, cure is carried through following anodising, referred to as closing. You will find numerous kinds of closing so the 2 many popular internationally and industrially recognised are:
know that hot seating: immersion in deep h20 with a heat of aproximatelly 95°C, that enables floor hydration on the aluminium oxide level and also shuts the porosity, therefore permitting much better opposition to oxidation.
cool sealing: immersion within a nickel fluoride formula at giving space heat. The nickel salts penetrate the porosity on the covering, strengthening oxidation opposition.
Even though warm closing is energy intensive since it should be taken care of at 95°C, it's more and more recommended, towards the detriment of nickel salts, that are carcinogenic which enable them to trigger epidermis allergic reactions. Within the foods business, for instance, nickel based closing can't be utilized.
Anodising resists oxidation wonderfully around exposure to alcohols, neutral solutions and hydrocarbons. Basic or acidic remedies dissolve the aluminium oxide, therefore negating the screen impact of oxidation safeguards. The dissolution number on the anodising level is proportional with the acidity or maybe basicity of the answer as well as much higher within the situation of fundamental remedies.
OX-W Hard anodizing is cure uniquely created to boost the by now great oxidation opposition of tough anodising. On certain alloys, it enables as many as thousand working hours of contact with basic salt squirt based on ISO 9227, without having the look of oxidation. OX-W is ideal for safeguarding alloys having an impressive silicon material, which might have troubles together with the regular anodising procedure.
Hardness, density and also put on opposition Hard anodising features a top hardness, that can vary based on the aluminium alloy employed.
The ISO 10074 specification describes the least hardness of particular alloys. The hardness is calculated based on ISO 4516 over a level using a thickness in between 25-50µm & a ton of 50g HV 0.05.
Alloy Vickers hardness
wrought alloys 400 HV
2000 series 250 HV
5000 sequence with Mg > 2% 300 HV
7000 series 300 HV
Casting alloys with Cu <2 % and also Si <8% 250 HV
The density, assessed around accordance with ISO 2106 with a covering of 50µm ± 5µm without closing, will need to have the following bare minimum values:
Alloy min. area density
wrought alloys 1100 mg/dm2
2000 series 950 mg/dm2
5000 sequence with Mg > 2% 950 mg/dm2
7000 series 950 mg/dm2
Casting alloys with Cu <2 % and also Si <8% 950 mg/dm2 The excessive hardness as well as compactness on the oxide level as well as the columnar system enable tough anodising to attain a top put on opposition, much higher compared to chemical substance nickel plating as well as much like tough chrome plating in thickness. The Taber Abraser is an exam which establishes the use of sliding coatings on coarse wheels. Based on ISO 10074, following 10,000 cycles, the mass damage has to be much less compared to the next values:
Alloy max. damage in deep mass
wrought alloys 15 mg
2000 series 35 mg
5000 sequence with Mg > 2% twenty five mg
7000 series 25 mg
Casting alloys with Cu <2 % and also Si <8% -
Roughness
Difficult anodising plays a role in minimal rise in area roughness and it is very apparent on surfaces with lower machining roughness.
OX-W difficult anodising has got the attribute of restricting the increased area roughness. Through the use of certain aluminium alloys as well as determining the proper working details, it's doable to always keep the last roughness beneath 0.5 Ra.
Foods call The conventional "EN 14392 Requirements for anodised goods for using in deep exposure to foodstuff" sets the demands for anodising remedies on aluminium components suitable for exposure to foods.
The remedies completed by Durox srl comply with EN 14392 if ever the following needs are met:
The substance make up on the aluminium alloys of the components to become anodised need to comply together with the demands of EN 601 or maybe EN 602, as much as relevant.
The anodising remedies need to encounter the closing stage that should be expressly requested.